Precision Layer Welding Machines
How to Choose the Right Precision Layer Welding Machine for Your Business
In today’s fast-paced manufacturing industry, precision is key. Whether you are in the automotive, aerospace, or electronics sector, having the right equipment can make all the difference in the quality and efficiency of your production process. One such piece of equipment that is essential for many industries is a precision layer welding machine.
precision wire layer winding machine is used to join thin metal sheets together with high accuracy and repeatability. These machines are commonly used in applications where precision is crucial, such as in the production of electronic components, medical devices, and automotive parts. With the advancement of technology, precision layer welding machines have become more sophisticated and versatile, offering a wide range of features and capabilities to meet the needs of various industries.
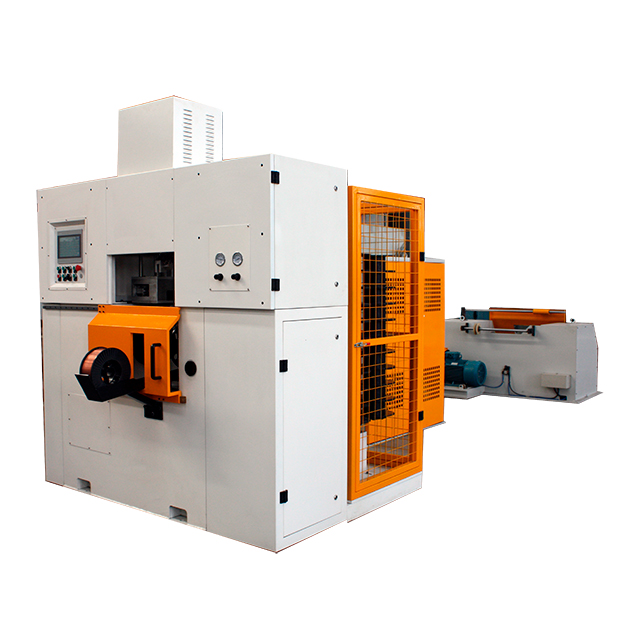
When choosing a precision layer welding machine for your business, there are several factors to consider to ensure that you are getting the right equipment for your specific needs. One of the most important factors to consider is the type of materials you will be working with. Different materials require different welding techniques and equipment, so it is essential to choose a machine that is compatible with the materials you will be using.
Another important factor to consider is the size and thickness of the materials you will be welding. Precision layer welding machines come in a variety of sizes and configurations, so it is crucial to choose a machine that can accommodate the size and thickness of the materials you will be working with. Additionally, consider the production volume and speed requirements of your business to ensure that the machine you choose can meet your production needs.
In addition to material compatibility and size considerations, it is also essential to consider the precision and accuracy of the machine. Look for a precision layer welding machine that offers high precision and repeatability to ensure that your welds are consistent and reliable. Some machines come with advanced features such as laser guidance systems and automated controls to help you achieve the highest level of precision in your welding process.
When choosing a precision layer welding machine, it is also important to consider the ease of use and maintenance of the machine. Look for a machine that is user-friendly and easy to operate, with intuitive controls and interfaces. Additionally, consider the maintenance requirements of the machine and choose a machine that is easy to maintain and service to minimize downtime and ensure the longevity of your equipment.
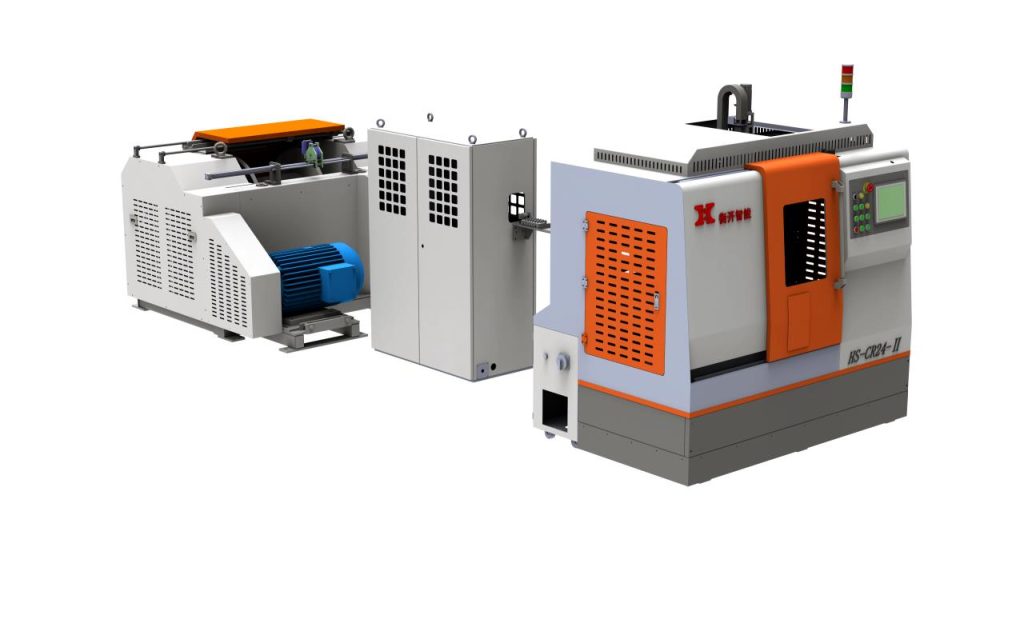
Finally, consider the reputation and reliability of the manufacturer when choosing a precision layer welding machine. Look for a manufacturer with a proven track record of producing high-quality machines and providing excellent customer support. Reading reviews and testimonials from other customers can also help you gauge the quality and reliability of the machine you are considering.
In conclusion, choosing the right precision layer welding machine for your business is essential to ensure the quality and efficiency of your production process. Consider factors such as material compatibility, size and thickness requirements, precision and accuracy, ease of use and maintenance, and the reputation of the manufacturer when making your decision. By taking the time to research and evaluate your options, you can find the perfect precision layer welding machine to meet your business needs and help you achieve success in your industry.
Tips for Maximizing Efficiency and Quality with Precision Layer Welding Machine Operations
Precision layer welding machines are a crucial tool in the manufacturing industry, allowing for the precise joining of metal components to create strong and durable products. To ensure that these machines operate at their highest efficiency and produce the highest quality welds, it is important to follow a few key tips and best practices.
One of the most important factors in maximizing efficiency and quality with precision layer welding machine operations is proper maintenance. Regular maintenance and cleaning of the machine can help prevent issues such as clogging, misalignment, and wear and tear on the components. This can help ensure that the machine operates smoothly and produces consistent, high-quality welds.
In addition to regular maintenance, it is also important to properly calibrate the machine before each use. This can help ensure that the machine is operating at its optimal settings and producing the best possible welds. Calibration should be done by a trained technician who is familiar with the specific machine and its requirements.
Another important tip for maximizing efficiency and quality with precision layer welding machine operations is to use the right welding parameters. This includes setting the correct voltage, current, and wire feed speed for the specific material and thickness being welded. Using the wrong parameters can result in weak or inconsistent welds, so it is important to carefully adjust these settings for each job.
It is also important to use high-quality welding wire and consumables when operating a precision layer welding machine. Using low-quality materials can result in poor weld quality and increased downtime for maintenance and repairs. Investing in high-quality materials can help ensure that the machine operates smoothly and produces strong, durable welds.
Proper training and supervision are also key factors in maximizing efficiency and quality with precision layer welding machine operations. Operators should be properly trained on how to use the machine safely and effectively, and should be supervised to ensure that they are following best practices and producing high-quality welds. Regular training and refresher courses can help keep operators up to date on the latest techniques and technologies in welding.
Finally, it is important to regularly inspect the welds produced by the precision layer welding machine to ensure that they meet quality standards. This can help identify any issues or defects early on, allowing for quick corrections and preventing costly rework. Inspections should be done by trained professionals who are familiar with the specific requirements of the job and can identify any potential issues.
In conclusion, maximizing efficiency and quality with precision layer welding machine operations requires proper maintenance, calibration, welding parameters, materials, training, supervision, and inspection. By following these tips and best practices, manufacturers can ensure that their precision layer welding machines operate at their highest efficiency and produce the highest quality welds. This can help improve productivity, reduce downtime, and increase customer satisfaction.