Automatic Welding Wire Precision Layer Winding Machine
Advantages of Precision Layer Welding in Industrial Applications
Precision Layer Winding Machine is a cutting-edge technology that has revolutionized industrial applications across various sectors. This advanced welding technique involves the precise deposition of material layer by layer, resulting in high-quality, durable welds that meet the stringent requirements of modern industries. In this article, we will explore the advantages of precision layer welding and how it has transformed the way manufacturers approach welding processes.
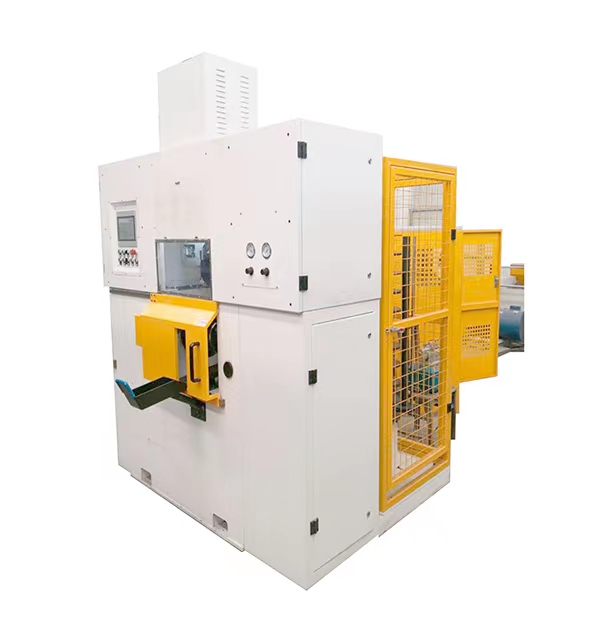
One of the key advantages of Welding Wire Precision Layer Winding Machine is its ability to produce welds with exceptional accuracy and consistency. By depositing material in thin layers, this technique ensures that each weld is uniform and free from defects. This level of precision is crucial in industries where the quality and reliability of welds are paramount, such as aerospace, automotive, and medical device manufacturing.
Furthermore, precision layer welding offers superior control over the welding process, allowing operators to adjust parameters such as heat input, deposition rate, and layer thickness with precision. This level of control enables manufacturers to tailor the welding process to meet specific requirements, resulting in welds that are optimized for strength, durability, and performance.
Another advantage of precision layer welding is its versatility. This technique can be used to weld a wide range of materials, including metals, alloys, and composites, making it suitable for a variety of industrial applications. Whether it’s joining dissimilar materials, repairing components, or adding material to worn parts, precision layer welding offers a flexible and efficient solution.
In addition to its accuracy and versatility, precision layer welding is also highly efficient. By depositing material only where it is needed, this technique minimizes waste and reduces the amount of post-weld machining required. This not only saves time and resources but also results in cost savings for manufacturers.
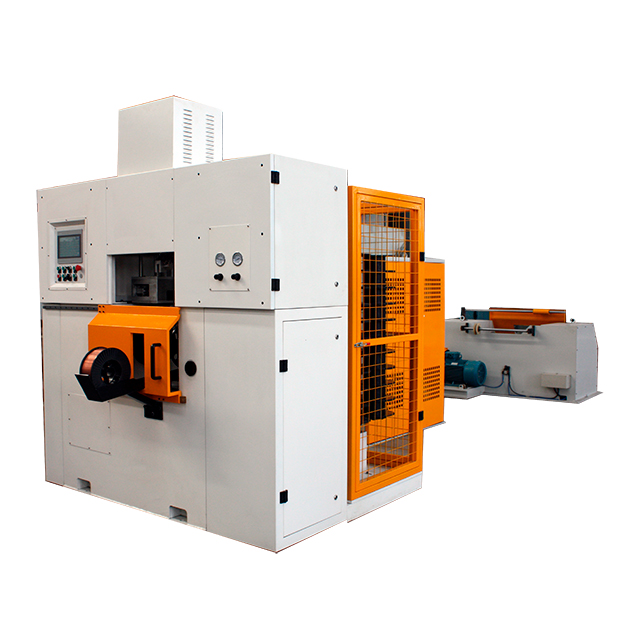
Moreover, precision layer welding is a non-contact process, which means that there is minimal distortion and heat-affected zone compared to traditional welding methods. This is particularly beneficial for delicate or heat-sensitive materials, where excessive heat can cause distortion or damage. By minimizing heat input and distortion, precision layer welding ensures that the integrity of the material is preserved, resulting in high-quality welds that meet the strictest standards.
Furthermore, precision layer welding is a highly automated process, which means that it can be easily integrated into existing manufacturing systems. This automation not only improves efficiency but also reduces the risk of human error, resulting in consistent and reliable welds every time.
In conclusion, precision layer welding offers a host of advantages for industrial applications, including exceptional accuracy, control, versatility, efficiency, and automation. This advanced welding technique has transformed the way manufacturers approach welding processes, enabling them to produce high-quality welds that meet the stringent requirements of modern industries. As technology continues to advance, precision layer welding is poised to become the go-to welding solution for a wide range of industrial applications.