Flux-cored Welding Wire Production Line
Tips for Properly Handling and Storing Flux-Cored Welding Wire
flux cored welding wire production line is a popular choice for welders due to its versatility and ease of use. However, proper handling and storage of flux-cored welding wire are essential to ensure optimal performance and longevity. In this article, we will discuss some tips for properly handling and storing flux-cored welding wire to help you get the best results from your welding projects.
When handling flux-cored welding wire, it is important to wear appropriate safety gear, such as gloves and safety glasses, to protect yourself from potential hazards. Flux-cored welding wire can be sharp and may cause injury if mishandled, so it is important to handle it with care. Additionally, be sure to inspect the wire for any signs of damage or contamination before use, as these can affect the quality of your welds.
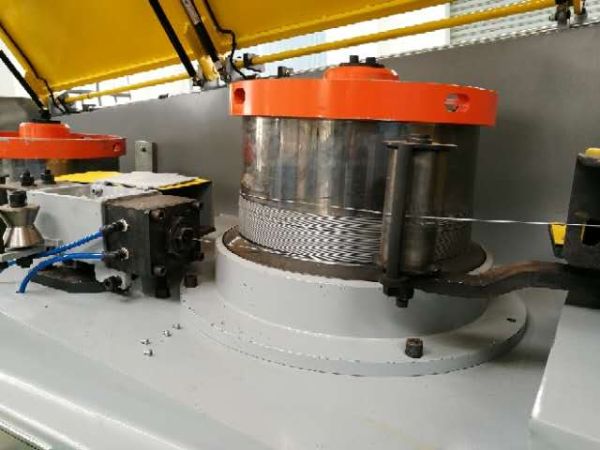
When storing flux-cored welding wire, it is important to keep it in a dry and clean environment to prevent rust and contamination. Store the wire in a cool, dry place away from moisture and humidity, as these can cause the wire to degrade over time. Additionally, be sure to keep the wire in its original packaging or a sealed container to protect it from dust and debris.
It is also important to store flux-cored welding wire in a vertical position to prevent it from becoming tangled or kinked. This will help ensure that the wire feeds smoothly through your welding machine and produces clean, consistent welds. Avoid storing the wire in a horizontal position, as this can cause it to become twisted and difficult to work with.
When handling flux-cored welding wire, be sure to feed it through your welding machine properly to prevent jams and tangles. Follow the manufacturer’s instructions for loading the wire into your machine, and be sure to adjust the tension settings as needed to ensure smooth feeding. Properly feeding the wire will help you achieve clean, consistent welds and prevent issues during the welding process.
In addition to proper handling and storage, it is important to use the right type of flux-cored welding wire for your specific welding application. There are different types of flux-cored welding wire available, each designed for specific welding processes and materials. Be sure to choose the right wire for your project to achieve the best results.
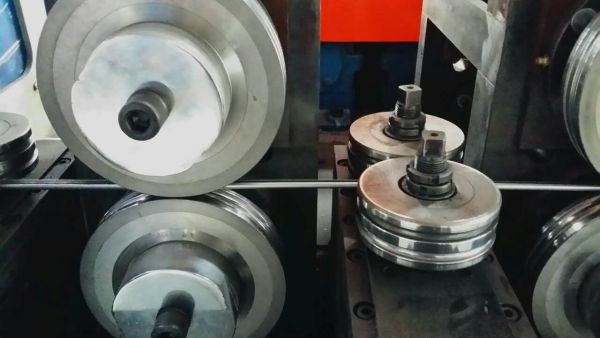
Finally, be sure to regularly inspect your flux-cored welding wire for any signs of damage or contamination. If you notice any issues, such as rust, kinks, or debris, replace the wire immediately to prevent issues during the welding process. By properly handling and storing your flux-cored welding wire, you can ensure that it performs optimally and helps you achieve high-quality welds.
In conclusion, proper handling and storage of Flux Cored Wire Production Line is essential to ensure optimal performance and longevity. By following these tips, you can help prevent issues during the welding process and achieve clean, consistent welds. Remember to wear appropriate safety gear, store the wire in a dry and clean environment, feed it properly through your welding machine, use the right type of wire for your project, and regularly inspect the wire for any signs of damage. With these tips in mind, you can make the most of your flux-cored welding wire and achieve professional results in your welding projects.
Comparison of Different Types of Flux-Cored Welding Wire
Flux-cored welding wire is a popular choice for welders due to its versatility and ease of use. There are several different types of flux-cored welding wire available on the market, each with its own unique characteristics and benefits. In this article, we will compare and contrast some of the most common types of flux-cored welding wire to help you make an informed decision when choosing the right one for your welding needs.
One of the most popular types of flux-cored welding wire is gas-shielded flux-cored wire. This type of wire is designed to be used with a shielding gas, typically a mixture of argon and carbon dioxide, to protect the weld from atmospheric contamination. Gas-shielded flux-cored wire produces clean, high-quality welds with minimal spatter, making it ideal for a wide range of applications.

Another common type of flux-cored welding wire is self-shielded flux-cored wire. Unlike gas-shielded wire, self-shielded wire does not require an external shielding gas, as it contains a flux compound that creates a protective atmosphere around the weld. Self-shielded flux-cored wire is often used in outdoor welding applications where wind and other environmental factors can disrupt the shielding gas flow.
In terms of performance, gas-shielded flux-cored wire typically produces cleaner welds with less spatter than self-shielded wire. However, self-shielded wire is more portable and easier to use in outdoor or remote welding situations where access to a shielding gas supply may be limited.
Another important factor to consider when choosing flux-cored welding wire is the type of flux compound used in the wire. Some flux compounds are designed to provide better penetration and weld strength, while others are formulated to reduce spatter and improve arc stability. It is important to choose a flux-cored wire with a flux compound that is compatible with the base metal you are welding and the welding process you are using.
In addition to the type of flux compound, the diameter of the flux-cored welding wire also plays a significant role in the welding process. Thicker wire diameters are typically used for welding thicker materials, as they can deposit more filler metal per pass. Thinner wire diameters are better suited for welding thinner materials, as they provide better control and precision.
When comparing different types of flux-cored welding wire, it is important to consider factors such as welding application, base metal type, welding process, and desired weld characteristics. Gas-shielded flux-cored wire is ideal for clean, high-quality welds in a controlled environment, while self-shielded flux-cored wire is more portable and versatile for outdoor or remote welding applications.
In conclusion, flux-cored welding wire is a versatile and efficient option for welders looking to achieve high-quality welds in a variety of applications. By understanding the differences between gas-shielded and self-shielded wire, as well as the importance of flux compound and wire diameter, you can choose the right type of flux-cored welding wire for your specific welding needs.