Flux-Coated Wire in Welding
Tips for Properly Welding with Flux-Coated Wire
Welding is a crucial process in various industries, from construction to automotive repair. One common method of welding is using flux-coated wire, which is a type of welding wire that has a flux coating on its surface. This flux coating helps to protect the weld from contamination and oxidation during the welding process. However, in order to achieve a strong and clean weld, it is important to follow some tips for properly welding with flux-coated wire.
First and foremost, it is essential to choose the right type of Flux Cored Wire Production Line for the job. Different types of flux-coated wires are designed for specific welding applications, so it is important to select the appropriate wire for the material being welded and the welding process being used. Additionally, it is important to ensure that the flux-coated wire is stored properly to prevent any damage to the flux coating, which could affect the quality of the weld.
Before starting the welding process, it is crucial to prepare the workpiece properly. This includes cleaning the surface of the metal to be welded to remove any dirt, rust, or other contaminants that could affect the quality of the weld. Additionally, it is important to ensure that the workpiece is properly aligned and clamped in place to prevent any movement during the welding process.
When welding with flux-coated wire, it is important to use the correct welding technique. This includes maintaining the proper arc length, travel speed, and angle of the welding gun. It is also important to ensure that the welding machine is set to the appropriate voltage and wire feed speed for the type of flux-coated wire being used.
During the welding process, it is important to pay attention to the appearance of the weld. A good weld should have a smooth and uniform appearance, with no gaps or irregularities. If the weld appears rough or uneven, it may be a sign that the welding technique needs to be adjusted.
After completing the weld, it is important to clean and inspect the weld to ensure its quality. This includes removing any slag or spatter from the weld and checking for any defects or imperfections. If any issues are found, they should be addressed before continuing with the welding process.
In conclusion, welding with flux-coated wire can be a highly effective method for joining metal pieces together. By following these tips for properly welding with flux-coated wire, you can ensure that your welds are strong, clean, and of high quality. Remember to choose the right type of flux-coated wire, prepare the workpiece properly, use the correct welding technique, and inspect the weld for quality. With practice and attention to detail, you can achieve excellent results with flux-coated wire welding
Advantages of Using Flux-Coated Wire in Welding
Welding is a crucial process in various industries, from construction to automotive manufacturing. It involves joining two or more metal pieces together by melting them and allowing them to cool, creating a strong bond. One common method of welding is using flux cored welding wire production line, which has several advantages over other welding techniques.
Flux-coated wire is a type of welding consumable that consists of a metal wire coated with a flux material. The flux serves multiple purposes during the welding process, such as protecting the molten metal from atmospheric contamination, facilitating the flow of the molten metal, and creating a protective slag layer that prevents oxidation. These properties make flux-coated wire an excellent choice for welding in various environments and conditions.
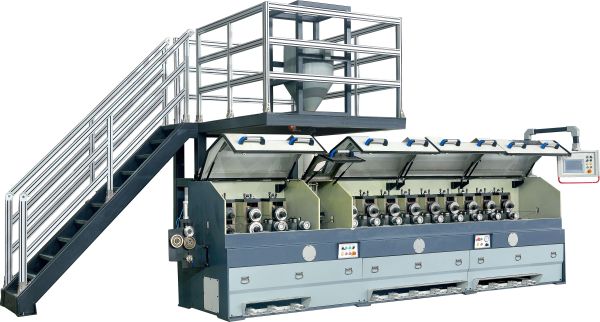
One of the main advantages of using flux-coated wire in welding is its versatility. Flux-coated wire can be used in a wide range of welding applications, from thin sheet metal to thick plates. It is suitable for both indoor and outdoor welding, making it a versatile option for welders working in different environments.
Another advantage of using flux-coated wire in welding is its ease of use. Flux-coated wire is pre-coated with flux, eliminating the need for additional flux materials during the welding process. This simplifies the welding process and reduces the risk of errors or inconsistencies. Additionally, flux-coated wire produces less spatter compared to other welding techniques, resulting in a cleaner weld and reducing the need for post-weld cleanup.
Flux-coated wire also offers improved weld quality compared to other welding techniques. The flux material in flux-coated wire helps to remove impurities from the molten metal, resulting in a cleaner and stronger weld. The protective slag layer created by the flux prevents oxidation and contamination, further enhancing the quality of the weld. This results in a more durable and reliable weld, making flux-coated wire an excellent choice for critical welding applications.
In addition to its versatility, ease of use, and improved weld quality, flux-coated wire also offers cost savings for welders. Flux-coated wire is more affordable than other welding consumables, such as gas cylinders or flux materials. This makes it a cost-effective option for welders looking to reduce their welding expenses without compromising on quality. Additionally, the reduced spatter and post-weld cleanup associated with flux-coated wire can save welders time and labor costs, further increasing its cost-effectiveness.
Overall, flux-coated wire offers several advantages for welders looking to achieve high-quality welds in a cost-effective and efficient manner. Its versatility, ease of use, improved weld quality, and cost savings make it an excellent choice for a wide range of welding applications. Whether you are a professional welder or a hobbyist, consider using flux-coated wire in your next welding project to experience the benefits firsthand.